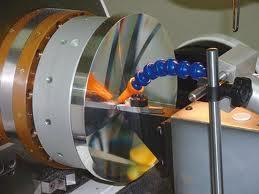
In the gear processing process, advanced blank forming process, stable and precise heat treatment process, and appropriate surface hardening process are the key factors for the final formation of gear products. For example, in the grinding process, there are several key steps: By using a grinding wheel with sharp edges and grinding the surface with small stress, the grinding feed can be increased, the grinding time can be shortened, the grinding efficiency can be improved, and the dressing of the grinding wheel can be extended. The spacing to reduce costs; by using appropriate grinding and dressing wheel parameters, to ensure that there is no grinding burn cracks and ensure the quality of the premise, use the highest possible grinding parameters to shorten the grinding time, improve grinding efficiency , To increase the output and ensure the accuracy and reduce the surface roughness; By using suitable grinding oil, under the premise of good lubrication and rust prevention, it is beneficial to reduce the surface stress of the grinding tooth surface, to avoid burn cracks, and to reduce the roughness. Decrease the degree of blocking the porosity of the grinding wheel to ensure the sharpness of the grinding wheel, reduce the dressing of the grinding wheel, reduce the amount of grinding wheel and reduce the cost.
In short, in the process of casting gears, we must pay attention to all kinds of problems in the design and processing, so as to ensure the quality of gears produced by casting.
Conveyor Sprocket,Transmission Sprocket,Chain Sprocket
Conveyor sprocket Co., Ltd. , http://www.transmissionsprocket.com