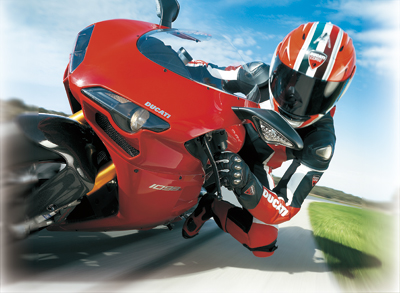
Figure 1 The Desmodromic system is a concept used by the Ducati engine to achieve high speed and high reliability since 1972. Ducati Motor, a world-renowned manufacturer of high-performance motorcycles, has accumulated long-term experience in processing and realized that it must be strictly Control of the importance of Desmodromic engine valuable parts processing, and decided to improve this processing. Ultimately relying on tool breakage detection produces a unique camshaft that prevents damage caused by tool breakage during machining. During the year, thousands of different tools are used, and there is always the risk of removing cracked or broken tools from the magazine, which can lead to very serious consequences. This problem is solved by using the Renishaw tool breakage detection system based on innovative non-contact laser measurement technology. The most important part of the camshaft production process was completed at two Stama machining centers. The two machining centers operate continuously throughout the year to produce camshafts for various Ducati engines (Figure 2). Fulvio Abbondi, Ducati Motor's manufacturing technologist, commented: “The shafts require high precision. The entire precision machining process is done in our factory. This is a very expensive part. It is made of special alloy steel, The cost of putting the blanks after the first roughing into the machine is very expensive."

Figure 2 The camshaft uses a special "rising ramp" non-traditional design

Figure 3 The Renishaw NC4 system is used to prevent broken tools from damaging very expensive parts – eliminating waste, avoiding rework and wasting time
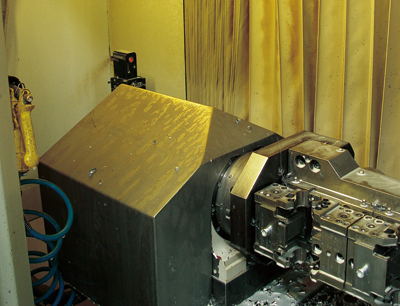
Figure 4 Renishaw Non-Contact Laser Tool Detection System Mounted Outside the Machine Work Area The consequences of tool breakage during the camshaft production process can be very serious, potentially resulting in significant waste, rework, and time lost. It is also possible to damage the spindle of the machine tool. This loss plus the cost of the special tool itself will amount to several thousand euros. Control Abbondi mentions the role of tool breakage detection. "It is very important to inspect the machining process on the machine. The Renishaw NC4 system is installed on two machining centers: After the tool is loaded into the spindle and ready for machining, it will immediately pass through the beam of the device at a specified height (Figure 3). If the cutting edge breaks, for example, it is not 100mm, but is 97mm long, the laser system will issue an alarm. Obviously, each tool has its own length, diameter, etc., and the system takes this factor into account when the tool passes the inspection beam. He continued: "With NC4, we can also examine the damage of small tools used to process the keys on the cam and other reference points, which is critical to the normal operation of the engine. Without the Renishaw system, the machine may be cutting. Running with broken blades can lead to catastrophic results, and because of the automatic breakage detection of the tool, an operator can easily manage two machine tools: all he needs to do is load the parts and ensure everything runs smoothly "Process control is critical to machining operations, as Abbondi said: "The first thing we do is install a set of A system provided by the machine tool manufacturer that can check the spindle motor's power." The system checks the degree of wear of the larger drill bit (used to drill the deepest hole), and the wear drill bit should be more stressed during machining. If the torque increases, it means that the tool is broken and an alarm is issued. But we also need to quickly and reliably detect tool breakage, even if the smallest damage is not missed, these breakages can often escape the inspection of most inspection systems. “Traditional contact detection systems have some disadvantages, and they are often not suitable for small tools—tools activate the device after touching the “button†or “rod.†The contact itself may also risk destroying the tool. This means that machining can only be done at low speeds. , which slows down the process and greatly lengthens the cycle time.The system must usually be installed in the work area, take up valuable space, and lead to possible collision danger, not to mention the low reliability due to easy clogging. Reasons to replace these devices with the Renishaw system Improvements with beam inspection laser technology have led to the development of non-contact detection systems that can safely measure smaller knives than ever before.A laser beam at the transmitter and receiver (Mounted on the side of the machine tool table or its opposite side) so that the light beam passes through the work area. When the tool passes through the light beam, the light flux detected by the receiver is reduced, and then a trigger pulse is generated. If the detected light flux is not When it is reduced, the system issues a tool breakage signal. Most global engine manufacturers are launching The return springs are used in the machine to close (exhaust and intake) valves, which then pull the valve back in. Ducati is an exception, and the company’s non-traditional Desmodromic system has many advantages, solving the problem of spring inertia and reducing With 30% operating wear, the Desmodromic distribution device makes the engine more reliable at high speeds.The engine can theoretically easily exceed 20,000 r/min.Desmodromic uses a mechanical system to close the valve, a concept that originated in the United States, but was too costly. However, the famous manufacturer of Bologna had another idea, and in 1972, the Desmodromic distribution device was combined in a two-cylinder engine, which has been used successfully for decades.The valve adopts a special cam instead of a simple spring. Closing, establishing the exact link between the valve and its position in all respects, the term Desmodromic comes from the Greek "desmòs", meaning "association".